Structures and Systems
Supply Chain Management
Against a backdrop of an expansion in our business areas, ITOCHU’s supply chain has become wider and more complex. There is now a further need for risk management concerning human rights, labor and the environment in the procurement of raw materials, producing areas, intermediate distribution and regions of consumption in addition to in the processes directly managed by us. We pay particular attention to the on-site management of suppliers who account for a relatively high share of our purchases. We view our consideration and sense of responsibility for these areas as matters of great importance to be addressed with high priority.
ITOCHU has established the Sustainability Action Guidelines for Supply Chains, and by conducting annual sustainability surveys and reviews as described below, we strive to confirm consistency with the guidelines and prevent the occurrence of problems. If we discover a problem, we aim for improvement through dialogue with the concerned supplier.
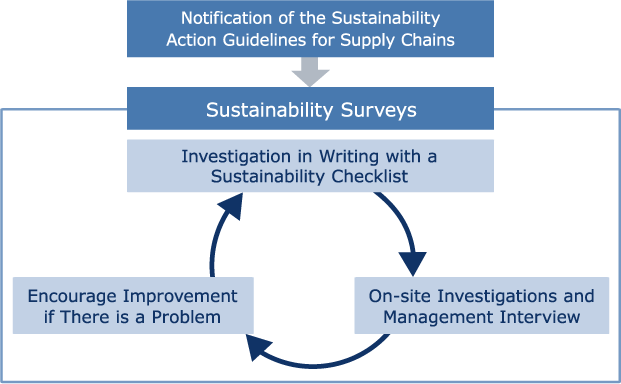
Sustainability Surveys
We have been conducting sustainability surveys since FYE 2009 to realize sustainable procurement and understand the actual conditions of suppliers. Each division company and applicable group company selects important suppliers based on certain guidelines (e.g., high risk countries, products handled and monetary value handled). The sales representatives of those division companies and representatives from overseas subsidiaries and operating companies then visit those suppliers to conduct interviews, in addition to a questionnaire format (sustainability checklist) with the seven core subjects of ISO26000 as essential survey items.
We conduct supply chain sustainability survey information seminar for employees who procure various products in a variety of countries ahead of the sustainability survey. We also provide training (buyer training) using the handbook to understand the Sustainability Action Guidelines for Supply Chains and ESG perspective that must be kept in mind in communication with suppliers.
Sustainability Checklist
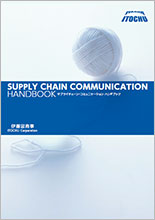
The Sustainability Checklist is used to conduct supplier surveys on their management of relevant sustainability risks. The Checklist is based on the seven ISO26000 core topics (organizational governance, human rights, labor practices, environment, fair business practices, consumer issues, community involvement and development) and is supplemented by department and product specific issues that we identified as relevant to our business and by extension our suppliers (see table below for our list of supplementary topics). Furthermore, based on opinions provided by external subject matter experts, we have constructed the survey questionnaire to consist of 19 core items centered around human rights and labor and environmental topics particularly associated to high sustainability risks – these items are our priority in supplier engagements.
Applicable Survey Criteria |
|
Main Questions Common to All Companies |
|
Procured Resource Type | Additional Survey Items |
Paper, Wood-chips, Timber |
|
Agricultural Crops |
|
Meat Products |
|
Natural Marine Products |
|
Apparel |
|
Palm Oil |
|
Coffee Beans |
|
We have also prepared a handbook on communication with suppliers. We are using this to inform our employees of how to communicate with suppliers. At the same time, we have set up a check system that enables employees to understand concretely the management situation in terms of the environment, human rights, labor practices and corruption prevention in important suppliers to give advice on making improvements. We will continue to conduct surveys and communicate with suppliers in the future to improve the awareness of our employees and to seek understanding and implementation from our suppliers.
Example Excerpt from the Handbook
Prohibition on forced labor

Companies must not force employees to work.
Forced labor means all labor forced on a person against his or her will. Examples include restrictions on an employee’s freedom to leave his or her job until he or she repays a debt to the company or restricting an employee’s freedom to leave his or her worksite under contract. Forced labor may be identified by asking employees what their work shifts are like, whether they have break times and whether they are able to eat meals. It may also be ascertained by observing their facial expressions. In a worst-case scenario, people are deprived of the freedom to live their lives; they have to live in a dormitory on the premises of the company’s factory and are not allowed to go outside those premises. It is also effective to check whether there are employees who have come to work from areas far away or other countries in a company. Employers must be prohibited from taking the originals of passports, IDs and work permits because this can lead to forced labor.
Reference
It is necessary to check for forced labor in factories in Japan as well as in emerging nations. In recent years, Japan’s Technical Intern Training Program (TITP) has been criticized by some from overseas. Accordingly, please also check whether suppliers in Japan employ anyone from overseas and whether there are problems in terms of working hours and wages.
FYE 2025 Sustainability Surveys
We conducted surveys on a total of 275 companies in FYE 2025. We did not discover any serious problems requiring an immediate response from those results. For 100% of business partners where concerns were identified during the surveys, we conducted follow-up investigations and confirmed that prompt corrective actions and countermeasures were implemented by these partners. Going forward, we will continue to seek the understanding of our business partners regarding our approach and maintain ongoing communication with them.
The companies surveyed over the past three years cover 61% of our business partners that meet our survey criteria.
All | ||||||||
Textile Company | Machinery Company | Metals & Minerals Company | Energy & Chemicals Company | Food Company | General Products & Realty Company | ICT & Financial Business Company | ||
FYE 2025 | 275 | 75 | 9 | 14 | 31 | 106 | 38 | 2 |
FYE 2024 | 305 | 74 | 8 | 20 | 31 | 104 | 65 | 3 |
FYE 2023 | 320 | 105 | 9 | 20 | 31 | 104 | 48 | 3 |
FYE 2022 | 288 | 65 | 9 | 20 | 31 | 107 | 53 | 3 |
FYE 2021 | 310 | 57 | 9 | 21 | 29 | 104 | 87 | 3 |
The Sustainability Management Division also visits and surveys important suppliers together with external experts as necessary.
Procured Resource Type | FYE 2023 | FYE 2024 | FYE 2025 |
Paper, Wood-chips, Timber, Timber Products | 38 | 52 | 32 |
Agricultural Crops | 36 | 31 | 31 |
Meat Products | 14 | 13 | 13 |
Natural Marine Products | 28 | 29 | 28 |
Apparel | 105 | 60 | 75 |
Palm Oil | 7 | 8 | 8 |
Coffee Beans | 19 | 23 | 26 |
Regional Breakdown of Number of Suppliers Surveyed
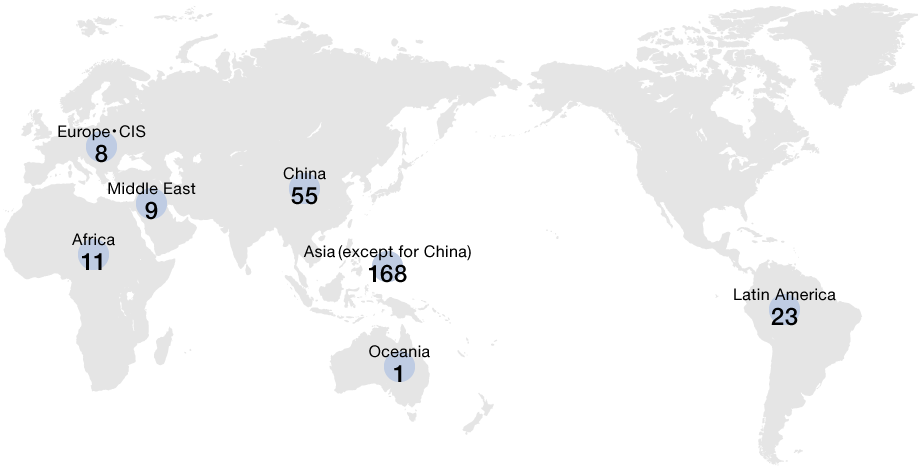
Human Rights Audits in the Poultry Industry in Thailand
Inspection of the CPF Saraburi Factory
We conducted a human rights audit targeting foreign workers in the Saraburi Factory (a chicken meat processed product factory) of Charoen Pokphand Foods Public Company Limited (CPF) — one of the main suppliers of the Food Company — accompanied by external auditors.
Recent years have seen an increase in cases where Japanese companies with Thai firms in their supply chain have been warned by NGO groups about human rights violations of foreign workers in the livestock and fishing industries in Thailand. We checked the factory for human rights risks in our supply chain through this audit.
This factory (slaughterhouse and food processing site) employs 1,300 Cambodians — equivalent to approximately 30% of its workers. That makes them an important part of the factory’s labor force. We checked a number of items in this audit. These included the extent of signage in Cambodian in facilities in the factory, a check of the evacuation routes, the attendance management situation, and the personal storage situation of passports and work permits. In addition, we also randomly chose some Cambodian employees actually working there and interviewed them about their actual working conditions.
This audit did not find any violations of the human rights of foreign workers, and reaffirmed there is sufficient consideration for human rights and the proactive approach CPF takes toward sustainability.
CPF has developed a safe working environment for its foreign workers.
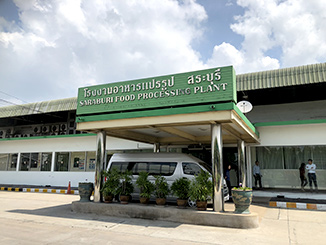
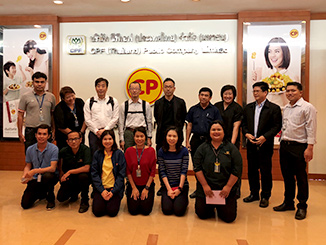
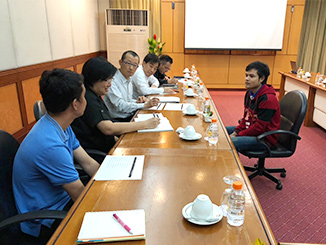
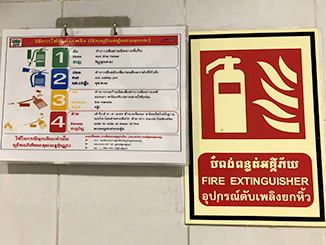
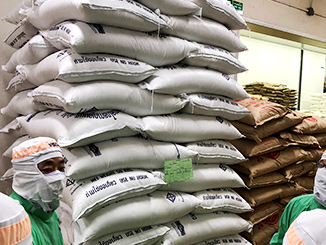
Regular Visits and Surveys of Food Processing Factories
The Food Company has been regularly visiting and surveying the food processing factories of its overseas suppliers since FYE 2012 in regards to imported foods under the initiative of the Food Safety and Compliance Management Office. In FYE 2025, we surveyed 369 overseas suppliers and inspected their food safety management system. We established a China Food Safety Management Team in Beijing in January 2015. With this, we have set up a structure to be able to audit our Chinese suppliers. We conducted regular audits and follow-up audits on 32 companies in FYE 2025. Please refer to Responsibilities to Customers to learn about our initiatives in detail.
Third-party Sustainability Audits of Ready-made Meal Manufacturers
Many foreign employees provide an important part of the workforce at factories to which FamilyMart, a group company, outsources manufacturing for ready-made meals.
Accordingly, in order to ensure a better work environment for a diverse workforce, FamilyMart conducts a self-assessment questionnaire (SAQ) for business partners involved in the distribution of FamilyMart products, consisting of approximately 200 items to evaluate whether employee safety, health management, and other aspects are being properly addressed. Additionally, in FYE 2025, FamilyMart conducted third-party audits of 18 factories, including raw material manufacturers. FamilyMart inspected compliance with human rights, labor, safety and health, environmental standards, and confirmed that there were no significant issues in each factory. FamilyMart will continue to take action to build a sustainable supply chain in collaboration with all its business partners.
Response to Suppliers in Violation of this Policy
When we have confirmed a case in which there has been a violation of the intent of any of our environmental or social policies, we request corrective action from the applicable supplier. Together with this, we conduct an on-site investigation to give guidance and improvement support as necessary.
In the FYE 2025 survey, the Sustainability Management Division carefully examined the answers from suppliers to key questions including the prohibition of child labor, the prohibition of forced labor and the payment of living wages, and identified issues that are necessary to share and to reconfirm with suppliers. As a result of this survey, the Sustainability Management Division requested the business departments in charge of the supplier to reconfirm the 42 extracted companies. The department in charge explained and shared the reconfirmation of these issues with the suppliers, and conducted a detailed survey of the suppliers’ responses to them.
As a result, it was determined that the reconfirmed issues were being addressed by each supplier, and no requests for corrective actions were made to suppliers in FYE 2025. Through this survey, suppliers actively report issues and engage with the business department involved. When a problem is identified, suppliers are requested to take corrective actions, thereby encouraging them to make efforts to correct the issue.
If it is judged that correction is difficult despite ongoing requests, we will reconsider our business with the relevant supplier, including regarding the continuation of the contract.
Key Questions | Request of Reconfirmation and Request of Corrective Action | |||
Questions | Checking Contents | Number of Reconfirmation | % (275 suppliers) | Number of Corrective Action |
Clarifying Responsibilities for Sustainability | A Sustainability Manager is appointed and the system for promoting sustainability is clear. | 12 | 4.4% | - |
Fair Operating Practices | We have established a policy and monitor the status of compliance with the policy by a person in charge. | 6 | 2.2% | - |
Preventing Information Leakage | We have established rules and informed all of our employees of the rules. | 1 | 0.4% | - |
Prohibition of Child Labor | We have clearly defined a minimum age for employees in light of the standards of the International Labor Organization (ILO) and we check the self-reported age of each person before employing them. | 3 | 1.1% | - |
Prohibition of Forced Labor | We have a policy of not using forced labor and we do not take a passport or a master copy of ID before employing them. | 4 | 1.5% | - |
Prohibition of Harassment | We have specified in writing that we prohibit harassment, and we have informed all of our employees to that effect. We also check whether any harassment actually occurs. | 6 | 2.2% | - |
Right to Organize and Bargain Collectively | We recognize the right of employees to organize and bargain collectively and regularly offer them opportunities, at least once a year, to communicate with the management regarding improving their labor environment. | 3 | 1.1% | - |
Prohibition of Discrimination | No restrictions on recruitment by gender, race, religion, etc. in recruitment conditions or requests to agent companies. | 2 | 0.7% | - |
Payment of Living Wage | We pay employees wages that exceed the legal minimum wage for each country. | 0 | 0.0% | - |
Working Hours | We have a system for the appropriate management of working hours throughout the entire business establishment. The working hours do not exceed the legal standards of the country. | 0 | 0.0% | - |
Taking Holidays | All of our employees have at least one day off every week. | 0 | 0.0% | - |
Identifying Dangerous Areas and Tasks | We acknowledge all labor accidents that have occurred, and we have a system under which we take measures to reduce their occurrence. | 0 | 0.0% | - |
Operating Procedures | We have operating procedures of occupational health and safety, and we review their contents at least once a year. | 0 | 0.0% | - |
Response to Labor Accidents | We acknowledge all labor accidents that have occurred, and we have a system under which we take measures to reduce their occurrence. | 7 | 2.5% | - |
Hygienic Ancillary Facilities | All of our facilities are kept in a sanitary condition. No issues were identified in the inspections undertaken by the local authorities or the like in the last five years or more. | 4 | 1.5% | - |
Treatment of Waste | We have a manual and apply the manual by reminding our employees of it at least once a year. | 29 | 10.5% | - |
Treatment of Exhaust Air and Discharged Water | We control them by applying standards that are stricter than the requirements of the local regulations. | 13 | 4.7% | - |
Procuring Raw Materials in a Responsible Manner | We ensure the traceability of more than 90% of raw materials, as far back as to the land of origin, and have a system in which we do not purchase them until we confirm that they are not problematic environmentally or socially. | 7 | 2.5% | - |
Development with Consideration for Local Residents | Grievance mechanism from local residents about noise, bad odor and environmental pollution of air and water, etc. | 7 | 2.5% | - |
Total Number of Suppliers | 42 | 15.3% | - |
Business Investment Management
The business activities of companies in which we invest must recognize and deal with their possible impact on the environment and society. To that end, we strive to understand ESG risks and work on preventative activities. We perform risk assessments on ESG in general through the utilization of a checklist and visits and surveys to formulate the necessary measures. These are continuously reviewed and improved in the framework of our environmental management system.
ESG Risk Assessment for New Business Investment Projects
It is compulsory in new business investment projects for the division making the application to use the ESG Checklist for Investments to evaluate the project in advance (perform due diligence). The division making the application looks at whether policies and structures have been established from a perspective of ESG. It also looks for the risk of a significant adverse effect on the environment, violation of laws and ordinances, and complaints from stakeholders. This checklist consists of check items that include elements of the seven core subjects* in ISO26000 — the CSR international guidelines.
The division making the application also then refers to review opinions based on risk analysis from relevant functional divisions (management divisions). If there are any concerns, it requests additional due diligence from external specialist organizations for matters requiring a professional point of view. The project is then only undertaken upon confirming that there are no problems in those results.
- Organizational governance, human rights, labor practices, the environment, fair operating practices, consumer issues, and community involvement and development
ESG Risk Assessment for the existing business (Group Company Fact-finding Investigations)
We have continued to conduct on-site visits and surveys in group companies since 2001 to prevent environmental pollution and risk assessment of labor practice. We have conducted investigations into a total of 298 offices in the world as of the end of March 2024.
These investigations inspect the factory and warehouse facilities, the situation of drainage to rivers, the environmental law and regulation compliance situation, labor practice, labor safety and human rights, and communication with the local community in addition to holding a question and answer session with management. We identify problems or demonstrate preventative measures. We then check to see whether the situation has been corrected.
Visit and Survey Report: DOLE PHILIPPINES Fact-finding Investigation
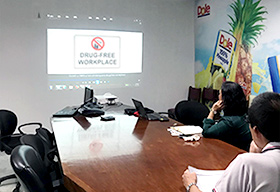
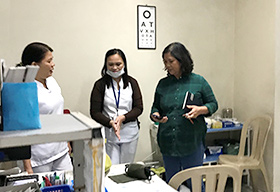
We visited and surveyed DOLE PHILIPPINES, a company which produces banana, pineapple and other fresh fruits and manufactures canned fruit in the Philippines, in January 2020. We performed a detailed check concerning the environment and labor safety related risk management and legal compliance situation (e.g., soil pollution, waste, chemical substance management and safety measures) based on the findings of external experts well-versed in the local laws and regulations. We confirmed that these matters are being appropriately managed. In addition, we confirmed that the company is proactively working on activities that contribute to society and the environment (e.g., biomass boiler on its premises and donations to local schools).