Sustainable Procurement: Policies and Initiatives by Product Type
Procurement Policies by Product Type
- Sustainable Procurement Policy on Natural Forests and Forest Resources (PDF 221KB)
- Natural Rubber Procurement Policy (PDF 167KB)
- Sustainable Palm Oil Procurement Policy (PDF 99KB)
- Cocoa Bean Procurement Policy (PDF 333KB)
- Coffee Bean Procurement Policy (PDF 278KB)
- Raw Material Tuna Procurement Policy (PDF 452KB)
- Commitment of Protecting Forests through Material Sourcing of MMCF (PDF 86KB)
Products of Relevance to Forest Conservation
ITOCHU handles the following products, which require careful consideration of forest conservation initiatives. In addition to the Sustainability Action Guidelines for Supply Chains, the following Procurement Policy establishes our approach to protecting and preserving natural forests, and our commitment to the sustainable use of natural resources. The Policy is subject to an annual review at minimum, with revisions made as necessary.
- Timber, timber products, raw materials for papermaking and paper products
- Natural rubber
- Palm oil
- Solid biomass fuel
Policy and Management Approach to the Preservation of Natural Forests and the Sustainable Sourcing of Forest Resources
Sustainable Procurement Policy on Natural Forests and Forest Resources
Management Approach
Every year, we report and receive approval on our targets and progress made to senior management. We also share suggestions from stakeholders including NGOs, and if any issue is identified, we review our measures and this Policy, as necessary.
Regarding palm oil, procurement based on this Policy is carried out by the Oil, Fats & Cacao Department of the Food Division within the Food Company – this department is therefore also responsible for the compliant procurement of palm oil.
Regarding timber, timber products, raw materials for papermaking and paper products, it is carried out by the Construction and Real Estate Division (Construction & Building Material Department) and the Forest Products, General Merchandise & Logistics Division (Forest Products & General Merchandise Department) within the General Products & Reality Company – these departments are therefore also responsible for the compliant procurement of these products.
Wood, Wood Products*, Papermaking Raw Material, and Paper Products
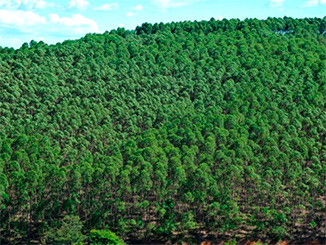
ITOCHU is engaged in the procurement, manufacturing, and distribution of materials for pulp and paper products, wood and wood products and woodchips. In order to ensure the protection of natural forests and sustainable use of forest resources, we aim for 100% procurement by FYE 2026 of certified material or material for which advanced management can be verified.
* Including board products such as plywood, MDF, particle board, etc.
Metsä Fibre Oy (Certification by FSC and PEFC)
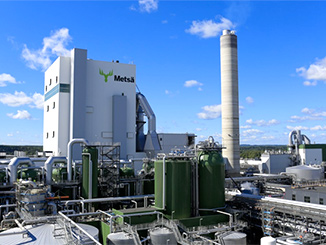
ITOCHU has a stake in Metsä Fibre Oy, a world-class softwood pulp manufacturer based out of Finland. Metsä Fibre Oy boasts an annual pulp production capacity of around 3.9 million tons. They have tapped ITOCHU as the exclusive distributor for their softwood pulp destined for Asian markets. The company manufactures pulp from 100% traceable forest resources of which 95% have received two certifications, namely the Forest Stewardship Council (FSC) and the Program for the Endorsement of Forest Certification Schemes (PEFC).
In Finland, pulpwood growth exceeds consumption, which allows for a long-term, stable supply of pulpwood. Through initiatives carried out with excellent partners such as this, we will promote the use of sustainable forest resources and continue to promote further strengthening of our business.
Certification of Traceability for Chinese Timber
Since 2013, ITOCHU KENZAI has been working to create a system for certifying the traceability of plywood manufactured in China. We asked the Japan Gas Appliances Inspection Association (JIA), a certification body, to evaluate the effectiveness of this system in 2020. It said we have ensured traceability appropriately in our main supply chain and are in compliance with the Law Concerning the Act on Promoting Green Procurement and the Clean Wood Act. This effort ensures traceability and that timber is managed throughout all processes within the supply chain, from the logging areas to the veneer and plywood factories, by obtaining logging permits and other evidence, auditing factories, observing the logging areas, and other means. With this, ITOCHU KENZAI was able to reliably ensure that no timber from illegal logging is used in around 40% of the plywood manufactured in China for which forest certification has not been obtained.
NGO Engagement (Responding to Identifications by an NGO about Illegal Logging and Human Rights Issues in Sarawak, Malaysia)
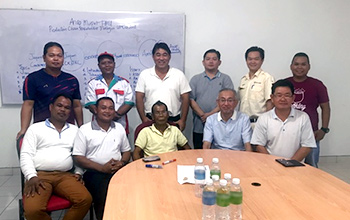
A non-governmental organization has pointed out problems with illegal logging and human rights in Sarawak, Malaysia. On a regular basis, we work to ascertain the situation through interview surveys of our supplier, the local government, the timber association, human rights lawyers, the human rights committee, local residents, local non-governmental organizations, forest consultants, and others.
We have not found the problems pointed out by the non-governmental organization through these surveys, but to eliminate concern, we have repeatedly requested that the supplier engage in specific initiatives. As a result, in recent years, the supplier has actively worked to obtain forest certification, and the number of certified forest areas has increased. Changes have also occurred in the local government in Sarawak, including reinforcement of regulations to eliminate illegal logging and announcement of measures to promote forest certification.
Performance Regarding Forest Certification and Legal Compliance
Performance of Timber and Timber Products*
ITOCHU evaluates its performance by classifying its timber and timber products into the following four categories based on forest certification and legal compliance. Category (A) signifies the highest level of sustainable procurement compliance, requiring FSC certification and/or PEFC certification – more specifically, it is defined as “(A) Timber handled by a certified forest supplier or timber approved by a certification body”.
- Including board products such as plywood, MDF, particle board, etc.
Classification Based on Legality | Item | Result | Target | |||
FYE 2023 | FYE 2024 | FYE 2025 | FYE 2026 | |||
Certified Materials or Advanced Management can be Confirmed | Forest Certification System | (A) Timber handled by a certified forest supplier or timber approved as a management material by a certification body (acquired FSC or PEFC certification) |
25% |
18% |
21% |
100% |
(B) Timber harvested in countries or regions assessed as “Low Risk” based on the forest certification system |
62% |
75% |
69% |
|||
Certification of Legality in the Clean Wood Act | (C) Timber whose legality has been confirmed by documents proving that it was cut in compliance with the laws of the place of origin*1 |
13% |
7% |
10% |
||
N/A | (D) Materials whose legality has been confirmed by “additional measures”*2 |
0% |
0% |
0% |
0% |
- Specifically, materials confirmed by an export license, certificate of origin, etc.
- Specifically, timber that was confirmed to be in compliance with laws by asking suppliers to provide a distribution channel
Sustainable Procurement Performance of Raw Materials for Papermaking
All raw materials for papermaking such as chips and pulp handled by ITOCHU Group have acquired FSC or PEFC certification as “materials handled by certified forest suppliers or materials approved as management materials by a certification body”.
Classification Based on Legality | Item | Result | Target | ||||
FYE 2023 | FYE 2024 | FYE 2025 | FYE 2026 | ||||
Certified Materials or Advanced Management can be Confirmed | Forest Certification System | Timber handled by a certified forest supplier or timber approved as a management material by a certification body (acquired FSC or PEFC certification) |
Chips |
97% |
100% |
100% |
100% |
Pulp |
100% |
100% |
100% |
100% |
- License No. FSC® C009841
Natural Rubber
ITOCHU is engaged in the business of processing natural rubber. Natural rubber is a natural resource indispensable in daily life. About 70% of the world’s consumption of natural rubber is used in tires. On the other hand, about 85% of the world’s production depends on small farmers found mainly in Thailand, Indonesia and elsewhere in Southeast Asia. It is expected that the demand for natural rubber will grow in the future due to global motorization. Against that background, it is essential to conduct business activities with even greater consideration due to issues such as deforestation and the infringement on the rights and poverty of small farmers. In response, ITOCHU has joined as a founding member of the Global Platform for Sustainable Natural Rubber (GPSNR), which was established in October 2018. We agree on the 12 principles stipulated by GPSNR and are cooperating in the development and operation of the Platform’s standards.
Moreover, we are utilizing our value chain to promote the PROJECT TREE initiative aimed at improving the traceability and sustainability of natural rubber. We will contribute to sustainability over the entire natural rubber industry through this project.
Participation in the GPSNR
In October 2018, ITOCHU joined the new Global Platform for Sustainable Natural Rubber as the only Japanese trading company founding member. This organization was established by car manufacturers, tire manufacturers and natural rubber processing companies, etc. involved in the natural rubber industry. Its members work together throughout their supply chain to establish traceability and achieve higher levels of sustainability.
PROJECT TREE Initiative
We are rolling out the PROJECT TREE initiative aimed at improving the traceability and sustainability of natural rubber. We are utilizing the value chain of the PT. Aneka Bumi Pratama (ABP) natural rubber processing company and the EUROPEAN TYRE ENTERPRISE LIMITED tire wholesale and retail company in which we invest to achieve this.
ITOCHU Techno-Solutions Corporation developed the traceability system utilizing the blockchain in this project. It is the first such attempt for traceability in the natural rubber industry.
ABP has been recording the origin information of the raw material by interviewing the suppliers. From now on, the transaction details, date and time, and location information for the natural rubber raw materials procured by ABP will be recorded on the blockchain by a smartphone app in this system. That information will then be displayed on a map. After that, ABP will process the natural rubber in its factories and sell it to tire manufacturers as natural rubber with place of origin information. We will implement a mechanism to pay compensation to raw material suppliers from a part of the sales of the Project supporting tires produced by those tire manufacturers. We will then distribute agricultural tools and fertilizers to small farmers who do not have smartphones or bank accounts. At the same time, we will conduct risk assessments including on the issue of modern slavery and provide training and support to improve productivity, including through the sharing of best practices, and address social issues. In addition, we will gradually implement improvement plans based on the results of risk assessments on the supply chain while receiving consulting and auditing from the Proforest and SNV international NGOs. This project is a concept we will expand to all stakeholders involved in natural rubber such as natural rubber processing companies in the same industry, tire wholesalers, retailers and automobile manufacturers, and consumers. We will aim to gradually roll out the approved tire products around the world starting with the highly-environmental conscious European region. Moreover, we also expect it will contribute to GPSNR policies and target achievement as well as to the requirement of the EU Deforestation Regulation (EUDR).
ITOCHU aims for sustainable growth based on our corporate philosophy of “Sampo-yoshi” (good for the seller, good for the buyer and good for society). We are also contributing to the Sustainable Development Goals (SDGs) in 2030 adopted by the United Nations.
- Release: ITOCHU Announces a Blockchain PoC for Traceability
- Release: ITOCHU Announces the Commencement of Commercialization of PROJECT TREE, the First Blockchain-based Natural Rubber Traceability and Sustainability Project in the World
- PROJECT TREE website
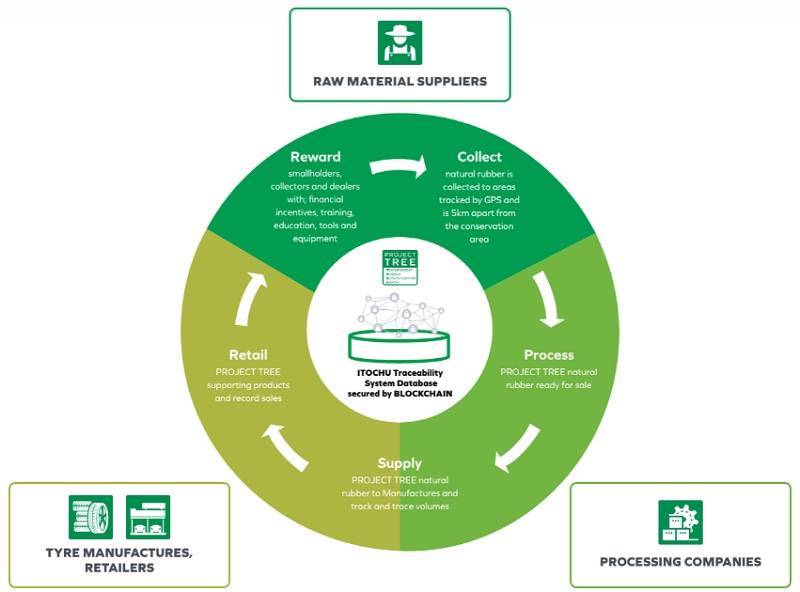
Performance Data on Natural Rubber
Category | 2022 (Jan-Dec) |
2023 (Jan-Dec) |
2024 (Jan-Dec) |
Target (2025) |
|
Natural Rubber Traceability | Up to Collecting Point | 4.5% | 7.0% | 11.5% | 100% |
Up to Smallholders | - | 0.4% | 7.6% | 33% | |
Capacity building, Sustainability training initiatives to small farmers | 3,934 people (Accumulatively 4,117 people) |
3,804 people (Accumulatively 7,921 people) |
11,991 people (Accumulatively 19,912 people) |
- |
Palm Oil
Palm oil has been associated with environmental destruction and human rights violations in relation to the development and production of plantations. ITOCHU is extensively engaged in the trade and distribution of palm oil but is not involved in the palm plantation business. However, based on our role in distribution, we recognize the importance of paying particular attention to this issue. For example, we are a member of the Roundtable Sustainable on Palm Oil (RSPO) and are working to fulfill our corporate social responsibility by taking responsibility and standing as a bridge between producers and consumers. We are also cooperating in the spread of certified oil other than RSPO, such as MSPO*1 and ISPO*2, in cooperation with industry groups.
In addition to having formulated the Sustainable Palm Oil Procurement Policy, we aim to preserve natural forests and ensure sustainable consumption of forest resources by promoting transparency in the supply chain and strengthening the sustainable palm oil procurement system.
- Malaysian Sustainable Palm Oil
- Indonesian Sustainable Palm Oil
Palm Oil Trading Supply Chain

Establishing Traceability
ITOCHU inspected our supply chain as a way to fulfil our corporate social responsibility. In doing so, we identified issues and solved them with the aim to achieve sustainable procurement and supply of palm oil. That allowed us to achieve one of our goals of achieving 100% traceability at the mill level by 2021. Going forward, we will aim to achieve our other goal of switching all the palm oil we procure to sustainable palm oil*1 by 2030. In particular, we aim to base our procurement on the NDPE principle (No Deforestation, No Peat, No Exploitation)*2.
- Sustainable palm oil: palm oil produced in a responsible manner which complies with NDPE policy and RSPO, MSPO, ISPO or any other equivalent standards
- No Deforestation, No Peat, No Exploitation (NDPE): zero deforestation, zero peatland development, zero exploitation
Sustainable Palm Oil Procurement Initiatives
ITOCHU aims for sustainable palm oil procurement and, based on the ITOCHU Group Human Rights Policy established in 2019, conducted human rights due diligence in FYE 2021 on major products of our Food Company, including palm oil. Since then, we have striven to understand the facts on the ground through our annual supply chain sustainability surveys. In FYE 2025, with the goal of further sustainable procurement of palm oil, a commodity requiring particular attention, we conducted human rights and environmental due diligence specific to palm oil with the cooperation of external experts.
This investigation covered 89 companies that are primary, secondary, and tertiary suppliers located in Malaysia and Indonesia. We conducted a self-assessment questionnaire (SAQ) in three languages: English, Malay, and Indonesian. Based on the results, we selected three companies for engagement to confirm the specific state of human rights risks and conducted more detailed interviews remotely.
To identify the relevant human rights issues, we confirmed certifications related to palm oil (RSPO, ISPO, MSPO certifications) and relevant regulations in each country, in line with the Group's Sustainable Palm Oil Procurement Policy. The survey items included child labor, forced labor, occupational health and safety, freedom of association and collective bargaining rights, discrimination, and environmental initiatives.
The investigation results did not confirm any items of concern for immediate risk or serious negative impacts on human rights. As an example of good practices, some business sites were found to be implementing appropriate preventive measures such as providing multilingual training on occupational health and safety. Many business sites were also confirmed to have established policies to prevent deforestation and efforts to reduce greenhouse gas (GHG) emissions. By sharing these good practices with suppliers, we aim to strengthen efforts throughout the supply chain. Each business site will continue to verify the response status and, where appropriate, engage to increase secondary and tertiary suppliers traceable back to plantations.
The Group will continue to cooperate with suppliers, identify human rights issues in advance, and address them seriously. Through continuous dialogue, we will encourage each supplier to address appropriate human rights issues.
Furthermore, by continuing regular efforts and improvements based on the human rights due diligence process, we aim to prevent, mitigate, and remedy real or potential negative impacts on human rights. Together with related companies, including suppliers, we will implement and strengthen initiatives to respect human rights, aiming to build a resilient value chain and achieve sustainable growth.
Survey Items | Child labor, forced labor, occupational health and safety, freedom of association and collective bargaining rights, discrimination, inhumane treatment, working hours and wages, grievance mechanisms, community-related initiatives, environmental initiatives (GHG emission reduction, deforestation prevention), anti-corruption, other items from external certifications/audits, etc. |
- Bold: Core labor standards of the ILO Declaration on Fundamental Principles and Rights at Work
Membership to the Roundtable on Sustainable Palm Oil (RSPO)
We joined the Roundtable on Sustainable Palm Oil (RSPO) in 2006, and respect the principles and standards set by the RSPO (such as the Principles and Criteria for the Production of Palm Oil) to promote transparency in the supply chain. We are working to strengthen the sustainable palm oil procurement system by expanding transactions with suppliers of raw material that have improved their traceability.
We confirm priority items and utilize them in procurement through sustainable procurement surveys, including on-site examinations, and direct engagement with suppliers.
In the course of our operations, we regularly review our procurement policy in cooperation with stakeholders such as business partners and experts. Information regarding this matter has been disclosed through the ESG Report, the Sustainability Action Plan, and the Annual Communication of Progress (ACOP).
- RSPO Supply Chain Certificate (PDF 237KB)
- Sustainability Action Plans
- The Annual Communication of Progress (ACOP)
Please also refer to the disclosed information below regarding ITOCHU’s initiatives.
Performance Data on Sustainable Palm Oil Procurement
Our goal is to transition all procured palm oil to sustainable palm oil by 2030. The following table shows the current progress of our initiatives and our targets.
Category | Result | Target | |||
2022 (Jan-Dec) |
2023 (Jan-Dec) |
2024 (Jan-Dec) |
2030 | ||
Volume of Handled Palm Oil | 352,000 tons |
386,000 tons |
376,000 tons |
||
<Main Supplier> | Malaysia |
Malaysia |
Malaysia |
Malaysia |
|
Indonesia |
Indonesia |
Indonesia |
Indonesia |
||
RSPO Members | 10/10 (100%) |
10/10 (100%) |
10/10 (100%) |
100% |
|
Suppliers Under NDPE Policy | 10/10 (100%) |
10/10 (100%) |
10/10 (100%) |
100% |
|
<Certified Sustainable Palm Oil> | |||||
RSPO Certified Sustainable Palm Oil | 19.24% |
28.60% |
35.90% |
||
<Traceability> | |||||
Traceable to the Mills | 100% |
100% |
100% |
100% |
Solid Biomass Fuel
ITOCHU procures Solid Biomass Fuels (woody biomass fuel and biomass solid fuel from agricultural residue) that have been legally verified by third-party certification systems such as Forest Management and Chain of Custody certification (PEFC, FSC,etc.), based on the Feed-in Tariff (FIT) program for renewable energy launched in July 2012 by the Ministry of Economy, Trade and Industry (METI).
ITOCHU conducts its own audit as needed by retaining an additional third party certification body (such as the Japan Gas Appliances Inspection Association (JIA), etc.)to ensure appropriate certification, thereby procuring fuel which has been verified as legal and sustainable.
In the event that a violation of our procurement policy is identified, ITOCHU immediately suspends any transaction with the supplier and requires it to take corrective actions, while providing guidance and support to the supplier.
Performance Data on Solid Biomass Fuel
Solid Biomass Fuels handled by ITOCHU have their legality, sustainability and traceability ensured by third-party certification systems such as Forest Management and Chain of Custody certification, etc.
Woody Biomass
Classification of Legality Basis | Item | FYE 2023 | FYE 2024 | FYE 2025 | |
Certified wood or highly controlled wood Forest | Forest certification, etc | Lumber whose legality, sustainability and traceability are ensured in accordance with third-party certification systems (such as PEFC, FSC and CoC certifications) or verified through voluntary initiatives utilizing third-party organizations (e.g., JIA) |
100% |
100% |
100% |
- License No. FSC® SCS-COC-000320, PEFC® CEF0610, SBP® SBP-06-51, GGL® GGL- 887567, JIA® JIA24-003 (ITOCHU’s certification number)
Biomass Solid Fuel from Agricultural Residues
Classification of Legality Basis | Item | FYE 2023 | FYE 2024 | FYE 2025 | |
Certified Product | Third-party certification, etc | Biomass solid fuel from agricultural residues (e.g., PKS) have ensured legality and sustainability through third-party certification systems such as GGL and others. | - | - | 100% |
- License No. GGL® GGL- 887567 (ITOCHU’s certification number)
- Based on the FIT/FIP program, obtaining certification related to sustainability (legality) became mandatory as of April 1, 2024.
Refer to:
Food
Cocoa Beans and Coffee Beans
ITOCHU handles cocoa beans and coffee beans as the raw ingredients of chocolate and coffee products. We operate processing/exporting business for coffee beans with UNEX (Guatemala), S.A. serving as our subsidiary. In the suitable areas to growing cocoa beans and coffee beans, the impact on human rights and the natural environment by plantation development and production has been identified. Accordingly, we have established procurement policies to fulfill our corporate social responsibility. Under these policies, we are promoting sustainable procurement in consideration of the environment and human rights.
Cocoa Bean and Coffee Bean Trading Supply Chain
Cocoa Beans

Coffee Beans

Overview of Cocoa Bean and Coffee Bean Dealings
Contents | Cocoa Beans | Coffee Beans |
Overview of Dealings | Trading |
Trading and processing/exporting |
Scope | ITOCHU Corporation and subsidiaries |
ITOCHU Corporation and subsidiaries (Including UNEX (Guatemala), S.A) |
Main Suppliers | Ghana and Latin America |
Brazil, Vietnam and Guatemala, etc. |
Main Sales Destinations | Japan and the U.S. |
Japan, Europe, North America and Asia |
Examples of Activities | Sustainable cocoa bean sourcing program |
Sustainable coffee bean sourcing Activities with UNEX (Guatemala), S.A Project with Farmer Connect SA |
Sustainable Cocoa Bean Sourcing Program
ITOCHU started handling sustainable cocoa beans in 2007. We will continue to further enhance the traceability of cocoa beans and work on strengthening our handling of cocoa beans to help with consideration for human rights and the environment, the eradication of poverty among farmers, and an improvement in living standards.
Performance Data on Sustainable Cocoa Bean Procurement
FYE 2024 | FYE 2025 | FYE 2031 Target | |
Sustainable Cocoa Bean | 64% | 65% | 100% |
Sustainable Coffee Bean Sourcing Program
ITOCHU has handled sustainable coffee beans over more than 15 years. In particular, we are working to strengthen our handling of sustainable certified coffee beans authenticated by organizations (e.g., UTZ, Rainforest Alliance and 4C) and defined by customers.
Activities of UNEX (Guatemala), S.A in Coffee Producing Area
ITOCHU is working on the following activities through UNEX (Guatemala), S.A – a subsidiary which collects coffee cargo in Guatemala.
Item | Content |
Technical Support for Small Farmers | Providing agricultural technology (e.g., methods of utilizing shaded trees and soil management) to improve the productivity of small farmers |
Support for Mobile Hospitals | Providing medical care to coffee producers and their families living in mountainous areas where there are no hospital nearby |
Support for Childcare Facility Management | Providing education, food and drink to the children of workers engaged in harvesting to prevent child labor |
Support for Female Producers | Conducting initiatives with a female-centered coffee producer group (COMAL) and providing agricultural guidance from the ethos of supporting women and gender equality |
Project with Farmer Connect SA
ITOCHU started project with Farmer Connect SA, a company aiming to build an IT platform to be able to browse coffee traceability information, in September 2019. This allows us to contribute to the growth of the coffee industry together with many companies responsible for coffee production, distribution and sales, and consumers.
Item | Content |
Strengthening Supply Chain Traceability | We record and store traceability information – from coffee bean cultivation, producing area, collecting point, blending and roasting to customers – with blockchain technology. |
Performance Data on Sustainable Coffee Bean Procurement
FYE 2023 | FYE 2024 | FYE 2025 | FYE 2031 Target | |
Sustainable Coffee Bean | 29% |
37% |
32% |
50% |
Dairy Products
ITOCHU stably procures and imports milk ingredients, cheeses and other dairy products from overseas dairy product suppliers with a production and quality control structure. The dairy product production and supply structure in Japan has been built centered on Hokkaido as part of agricultural policy. However, in response to the increase in consumption of dairy products in Japan in recent years, import opportunities have been steadily increasing under trade liberalization agreements (e.g., the TPP and EPA).
Producers’ organizations and companies in major dairy product producing countries (New Zealand, Australia, Europe, North America and South America) have gradually started initiatives to build a production structure enabling sustainable growth. We will strive to understand the initiatives of major production areas and suppliers through regular and surveys by sales representatives and work to further build relationships. This is so that we can continue to deliver safe and secure dairy products in the future.
Ensuring the Safety of Raw Milk
Ensuring the safety of raw milk in dairy product supply chains is paramount. We have a structure in which raw milk milked and collected by dairy farmers and then brought to dairy product factories is subject to antibiotic contamination tests at the acceptance stage. This means we only use raw milk confirmed to be safe.
In addition, manufactured cheese, butter and skim milk powder (excluding powdered milk) are individually packed in manufacturing factories mainly in 10 kg or 20 kg cardboard boxes for cheese and butter, and 25 kg paper bags for skim milk powder. The manufacturing date is then printed on these. Accordingly, it is possible to trace products up to the date of their production date in the manufacturing factory.
The standards for hormones and antibiotics used to breed beef and dairy cattle are established by the relevant organizations in each country. Each dairy product manufacturer then sets its own self-management regulations based on those standards.
Initiatives for the Sustainability of Ranches
An example of these initiatives is that basically dairy cows are raised by grazing in New Zealand – an important supply base for ITOCHU. The cows are bred while changing their grazing land regularly so that ranches do not fall into ruin. We are promoting such initiatives to help improve productivity.
Moreover, we have started the product development and distribution of grass-fed butter produced from beef and dairy cows raised eating only grass in New Zealand. Regular butter is made with the milk of cows raised mainly on grains. In contrast to this, grass-fed butter is made with the milk of cows raised eating only grass or grass of at least a certain ratio. This has the advantage of reducing the financial burden on dairy farmers.
Meat
Surveys of Beef Supplier Food Safety Management Systems
As a general rule, ITOCHU verifies whether beef suppliers for import transactions have HACCP certification or GFSI (Global Food Safety Initiative)-recognized certification. GFSI is a non-profit organization that involves globally expanding food companies and promotes food safety.
Initiative Participation
Companies in wide-ranging lines of businesses – from producers to retailers – are participating in an initiative called the Global Round Table for Sustainable Beef (GRSB) with the aim of sustainable beef production. ITOCHU has built business relationships with multiple companies participating in the GRSB. We are exchanging information with them on the latest trends.
Performance Data on Traceability
ITOCHU considers the safety and security of food as our number one priority, based on the key assumption that we are able to thoroughly trace the products we deliver to our customers back to their producers.
We have a 100% “traceback” system for all meat (beef, pork, chicken) suppliers (mainly overseas) allowing us to trace back products up to their production stage.
Content | Performance | ||||||
2022 | 2023 | 2024 | |||||
Volume of Handled Meat | About 130,000 tons |
About 130,000 tons |
About 140,000 tons |
Ensuring Traceability at HyLife Group Holdings
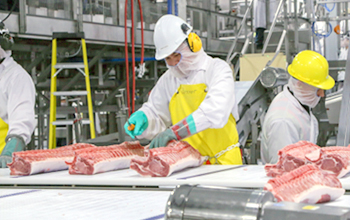
HyLife’s integrated production includes pig farms, mixed feed factories and pork processing, enabling supply chain management and coordination in-house. HyLife has utilized this production structure to achieve a stable supply of safe and secure, high-quality and traceable products. In addition, it is possible to communicate the individual needs of customers to pig farms through such integrated production. Hylife has established a specialty program customized for Japan that has been well-received in the market. Currently, it is one of the largest exporters of chilled pork to Japan in North America.
Promotion of Animal Welfare at Group Companies and Suppliers
Regarding its meat products, the ITOCHU Group believes that it is important for its livestock to be kept in a comfortable environment and to reduce stress and disease. Based on the belief that these animal welfare initiatives will lead to improved productivity and safer livestock products, we are working with meat-related Group companies and suppliers to promote initiatives for the humane handling of livestock in accordance with local laws.
Initiatives by Meat Supplier
Respecting Animals is a HyLife Core Value and the obligation and responsibility of all employees.
HyLife provides optimal environmental conditions for the animals in our care providing climate controlled housing, nutritionally balanced diets and veterinary animal health oversight.
All employees receive comprehensive training in the proper care and handling of animals and farms are operated in accordance with the Canadian Code of Practice for the Care and Handling of Pigs and are certified under the Canadian Quality Assurance Program.
Initiatives at Group Companies
In 2023, Group company Prima Meat Packers, LTD. established the Group Procurement Policy to promote responsible procurement that is safe and secure and takes into consideration the global environment, human rights, and animal welfare. At the new farm in Miyagi Prefecture, which began operations in 2023, we have created an environment to alleviate the stress of pigs. In the future, we are considering the introduction of free stalls when building or expanding a new pigpen on another farm, and we plan to promote animal welfare measures.
Marine Products
We mainly handle skipjack and yellowfin as marine products. In Indonesia, we operate the PT. Aneka Tuna Indonesia (ATI) canned tuna factory in a joint venture with partners. We have established voluntary management regulations for tuna. We are dedicated to our policy of only procuring skipjack and yellowfin that have been appropriately managed by fishing organizations.
Targets
The acquisition of MSC*1 certification is limited among fishermen for the highly migratory fish of skipjack and yellowfin at present. Under these circumstances, we are also encouraging fishermen to acquire this certification in the trade of skipjack and yellowfin for the raw ingredients in canned food products. We aim to increase MSC raw ingredients to 15,000 tons a year by FYE 2026.
The quantity of pole and line fished*2 raw ingredients in ATI was increased from 8,000 tons in FYE 2014 to 16,600 tons in FYE 2025 (39% of the total quantity handled by ATI). It has become one of the few canned tuna factories in the world that uses a large amount of pole and line fished raw ingredients. We will continue to work to secure, maintain and increase pole and line fished raw ingredients.
- The Marine Stewardship Council (MSC) is an international NPO established in 1997 to work on spreading sustainable fishing. Its headquarters are located in London, England.
- Pole and line fishing is a method of fishing by catching one fish at a time. It is a sustainable fishing method that does not involve the catch of large quantities of fish at one time. It is said that it is an environmentally friendly fishing method because it is also possible to avoid the bycatch of non-targeted fish.
Sustainability Surveys for Marine Resource Suppliers to Ensure Responsible Procurement Practices
We regularly visit and survey our suppliers. This is so that we responsibly procure marine resources for all the marine products we handle. We also promote cooperation with various fishing organizations. Every year, those in charge of sales visit and survey 28 suppliers applicable to our internal selection criteria in cooperation with our Food Safety and Compliance Management Office. This is for the regular visits and surveys on our suppliers to responsibly procure marine resources. We also engage in business after confirming that suppliers are appropriate from a viewpoint of ESG.
Regarding bonito tuna, which we handle in vast quantities, we prohibit procurement from IUU fishing (concerning illegal fishing: “Illegal, Unreported and Unregulated”). We only procure and purchase marine products whose origin is clearly traceable to fisheries that are properly managed by the Western & Central Pacific Fisheries Commission (WCPFC).
Certifications and External Stakeholder and Initiative Participation
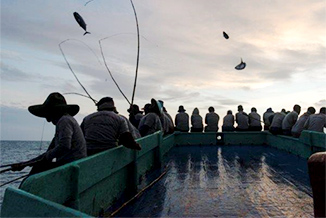
We acquired distributor certification and chain of custody certificate (CoC)*1 certification from the Marine Stewardship Council (MSC) in March 2018.
We joined the Organization for the Promotion of Responsible Tuna Fisheries (OPRT) in 2012 in the tuna business. This is an organization that was established for the sustainable use of tuna resources. We are now promoting initiatives that comply with our aforementioned voluntary management regulations.
ATI is strengthening its handling of pole and line fished raw material– considered to be the most environmentally friendly skipjack and yellowfin fishing method. The need for products made with pole and line fished raw material is growing every year in markets with a high interest in sustainability (e.g., the U.K. and Australia) for the canned tuna market as well. It is our policy to strengthen our handling of pole and line fished products manufactured by ATI.
ATI joined the Indonesian Association of Pole & Line and Hand Line in 2014. It is offering its cooperation such as by providing data. This data is used in the Fishery Improvement Program (FIP)*2. ATI is also cooperating for the acquisition of MSC in Indonesia. Moreover, it joined an international organization called the International Seafood Sustainability Foundation (ISSF)*3 in 2016. ATI is offering its cooperation such as by providing information in the same way as it does with the Indonesian Association of Pole & Line and Hand Line.
- Chain of custody certificate (CoC) is certification for processors and distributors. This is to ensure the traceability of MSC certified marine products and other products in the management of processing and distribution processes specified by MSC.
- The Fishery Improvement Program (FIP) is a project in which small fishermen finding it difficult to acquire MSC certification and market stakeholders cooperate and work together aiming for sustainable fishing under the goal of future MSC acquisition with MSC compliant fishing methods.
- The International Seafood Sustainability Foundation (ISSF) is an organization running under the aim of sustainable skipjack and yellowfin fishing. It was launched in response to an appeal by major canned tuna operators in 2009.
Performance Data Related to Certification
Item | FYE 2023 | FYE 2024 | FYE 2025 | Target (FYE 2026) |
||
Fisheries Raw Materials Handled by ITOCHU | MSC and/or COC Certified Fisheries Raw Materials | MSC/COC Quantity | 7,500 tons |
10,000 tons |
12,500 tons |
15,000 tons |
Percentage of MSC/COC Certified Raw Materials | 4% |
6% |
6% |
8% |
||
Bonito Tuna for Canned Tuna | ATI Fishing Line | ATI Single Fishing Raw Material Quantity | 13,000 tons |
13,700 tons |
16,600 tons |
21,000 tons |
Textile Raw Materials
In recent years, the trend for sustainability has been gradually penetrating the fashion market. For example, global fashion brands have declared that they will switch to using environmentally friendly materials (e.g., organic cotton, recycled polyester etc.) for the materials they procure as an initiative to develop the labor environment in the supply chain and to deal with the disposal of clothing and other problems. This issue is particularly important to us given that ITOCHU was founded as a textile raw materials trading business, which remains a cornerstone of our company to this day as a part of the Fashion Apparel Division. Therefore, in our textile business we have made it our policy to shift our raw materials portfolio to environmentally friendly resources and build traceability capacity from raw materials procurement to distribution to manufacturers. Our target for this policy set for 2025, which was to make 50% of the textile raw materials, handled by the section in charge*, traceable and environmentally friendly , as well as to switch 80% of polyester to recycled polyester, was achieved ahead of schedule in 2024.
- The textile raw material section
Organic Cotton Procurement in India
Traceability in Organic Cotton Procurement in India

When we procure organic cotton in India, we first purchase raw organic cotton that comes with a certificate from a ginning (work to separate the seeds and fibers after harvesting raw cotton) factory in India that has acquired GOTS certification. We deliver that raw organic cotton to spinning factories that have acquired GOTS certification in India or Asia. Finally, we purchase the yarn spun in those spinning factories and sell it to weaving/knitting factories in Japan and overseas. Furthermore, with regards to the traceability of organic cotton, we have implemented measures to leveraging our vast network and experiences to facilitate our cotton farmers in India to shift toward organic farming methods and to support certification acquirements (such as the GOTS certification*) at our cotton mills and ginning factories. Given these initiatives, we have achieved 100% traceability in the organic cotton and the cotton in the 3-year transition period to the organic cotton.
- GOTS certification: a set of comprehensive standards that certifies products made from organic textile. The standards cover the following items: use of certified raw materials and their traceability, control systems to limit or prohibit designated chemical inputs (dyes and auxiliaries) and accessories, separation and identification systems, environmental management, contamination and residue testing, and social criteria (possible sources of information: interview with management, confidential interviews with workers, personnel documents, physical on-site inspection, unions/stakeholders).
Performance Data on Organic Cotton Procurement
All organic cotton is GOTS certified and traceable.
Item | FYE 2023 | FYE 2024 | FYE 2025 |
Organic Cotton Handled (1,000 kg) | 800 |
1,876 |
2,060 |
Percentage of Cotton Trade | 30% |
85% |
90% |
Traceability of Organic Cotton | 100% |
100% |
100% |
GOTS Certification of Organic Cotton | 100% |
100% |
100% |
Expansion of Environmentally Friendly Materials
Our Apparel Division has been working on branding, commercializing and proposing natural materials for several years. In response to the recent momentum for conversion to sustainable materials in the global apparel market, we are also working to expand our use of environmentally friendly materials.
We launched the RENU Project with the aim of realizing a recycling-oriented society in 2019. The first product in that project came from us developing recycled polyester.
We started the trial deployment of a cellulose material derived from coniferous forests called Kuura in March 2021. This is a new material we have jointly developed with a major company in the Finnish forest industry called the Metsä Group. Using renewable energy in the manufacturing factory and using a special solvent in the manufacturing process for this product has helped us to reduce our burden on the environment. In addition, we have established traceability that even includes the timber for this. These efforts have led to this product attracting attention as an innovative sustainable material.
We will continue to accelerate the pace of our cooperation with global companies toward our increasing use of environmentally friendly materials in the future. At the same time, we will work to acquire certification in the spinning, weaving/knitting and sewing processes and to expand internal cross-company business toward establishing branding and traceability up to commercialization – our medium term target.